Tesio Cooling Systems approach to quality, verified throughout the entire product life cycle, is focused on the following aspects:
QUALITY
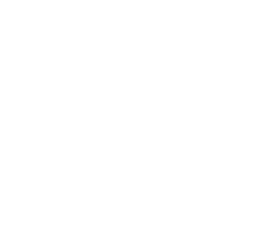
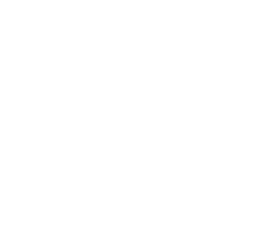
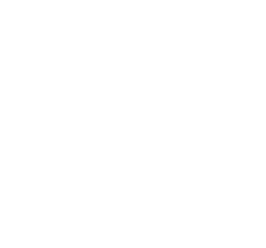
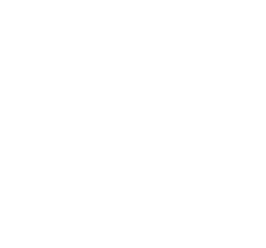
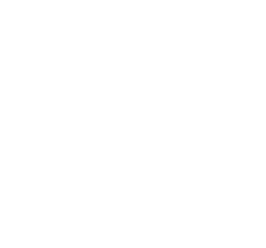
RELIABILITY
SATISFACTION OF INTERESTED PARTIES
CONTINUOUS IMPROVEMENT
The company processes and quality system of Tesio Cooling Systems are certified by RINA and comply with both the ISO 9001:2015 standard and the IRIS Certification® rev. 04 standard, based on ISO 22163: 2023 for the railway market, which has enriched the company's curriculum since 2011.
The quality system is also integrated with the environmental system and is certified by INTERTEK in accordance with ISO 14001:2015.
The quality requirements of our welding processes and their design are certified by LRQA and comply with UNI EN ISO 3834-2 and EN 15085-2 (level CL1), the standard for welding in the railway industry.
1. TECHNICAL-COMMERCIAL PHASE
In response to a request for evaluation issued by the customer, the first step focuses on the feasibility analysis of the article requested with the proposed heat exchange characteristics and the verification of the technical-commercial feasibility of the product with attention to the customer’s specifications;
2. DESIGN AND PROTOTYPING PHASE
The company know-how is managed through standardized methodologies. All the design elements are taken care of: from functional dimensioning to calculation, to the selection of the most appropriate production technologies for the realization. The care of the prototyping phase is the first moment of operational control, in which all the design elements are checked on site;
3. EXPERIMENTAL TESTS PHASE AND VALIDATION
Once the prototype has been made, the experimental tests on the product, carried out thanks to the internal laboratories, verify all the functional performances and contribute decisively to the validation of the object which must meet all the technical and quality requirements of the customer;
4. SERIAL PRODUCTION PHASE
Production engineering ensures efficient and effective processes during the production of the product, guaranteeing control during all construction phases. An attitude for continuous improvement allows us to seek ever better construction efficiency;
5. CUSTOMER CARE AND AFTER MARKET PHASE
customer satisfaction is guaranteed not only with product compliance, but with the responsiveness and high quality standard of the services that accompany it. Once the product’s life cycle is over, the company guarantees that the spare parts required in the years to come will maintain the same quality standards agreed for the originally validated product.